Ремонт тормозного цилиндра грузового вагона, техпроцесс на Vagonmaster
Тормозная система грузовых вагонов должна быть эффективной, чтобы обеспечивать остановку поезда в пределах нормативного тормозного пути. Однако при интенсивной эксплуатации железнодорожных вагонов наблюдается износ тормозных механизмов, поэтому они нуждаются в ремонте. При этом главная задача – устранить износившиеся трущиеся пары в вагонах, а также предупредить возможность поломки тормозных устройств во время работы. Благодаря этому можно наладить бесперебойную и безаварийную работу всех элементов в течение определенного срока.
Ремонт тормозного цилиндра
Тормозной цилиндр – один из важных компонентов системы, где энергия сжатого воздуха преобразовывается в механическую. Затем она передается с помощью тормозной рычажной передачи на колодки, прижимая их к ободу колеса. Тормозные цилиндры обеспечивают работоспособность при температуре ±55 °С. Корпус тормозных цилиндров выполнен из надежных и долговечных материалов – чугуна либо стали. Гарантийный срок работы тормозных цилиндров – два года со дня начала эксплуатации (со знаком качества четыре).
Внутри корпуса тормозного цилиндра есть отпускная пружина, поршень с резиновой уплотняющей манжетой и войлочным смазывающим кольцом, а также шток. В задней крышке тормозного цилиндра, которая крепится к корпусу с помощью большого количества болтов, есть два отверстия: первое – используется для подвода сжатого воздуха, а второе, заглушенное пробкой – применяется для установки манометра во время эксплуатационных испытаний. В передней крышке есть специальное небольшое отверстие, которое используется для слива конденсата, а ее горловина оснащена резиновой шайбой, защищающей от пыли.
Описание тормозной системы грузового вагона
Тормозное оборудование грузового вагона – это устройства, которые создают искусственное сопротивление движению поезда для регулировки скорости его движения или остановки. Благодаря ему осуществляется искусственное противодействие вращению колес.
Согласно правилам, грузовые вагоны обязательно должны быть оснащены автоматическими пневматическими фрикционными тормозами и стояночными с ручным либо автоматическим приводом. Допускается также оборудование вагона электропневматическим тормозом. Причем все элементы тормозной системы важно своевременно чистить, а также регулярно проверять их, чтобы убедиться в их надежности и управляемости.
В процессе фрикционного торможения колодки вагонов контактируют с дисками колесных пар, и в результате возникает трение, с помощью которого кинетическая энергия превращается в тепловую, а затем рассеивается в атмосфере. При этом в вагонах задействованы три типа устройств:
- Пневматические, с применением силы сжатого воздуха.
- Электропневматические, где управление происходит с помощью тока, который заставляет тормозные колодки прижиматься к колесам.
- Механические, которые часто применяются как запасные.
Кроме того, тормозные устройства грузовых вагонов могут быть с авторежимом либо без него.
Есть несколько видов тормозных колодок:
- Чугунные. Основные достоинства таких тормозных колодок – устойчивость к влаге и высокий коэффициент отведения тепла. Наиболее безопасными считаются тормозные механизмы из чугуна, ведь они не слишком сильно нагреваются.
- Композиционные. Это металлическая основа с фрикционными элементами. Преимущества композиционных тормозных колодок – высокий коэффициент трения и износостойкость, благодаря добавлению асбокаучука, а также связующих веществ. Они в несколько раз прочнее чугунных и увеличивают тормозную эффективность поездов.
- Тормозные колодки для определенных единиц состава. Это варианты со специальным исполнением, ведь поверхности, которые непосредственно контактируют с рельсами, выполнены из металлокерамики. Это достаточно дорогие тормозные колодки, но надежные и долговечные.
При эксплуатации тормозных колодок возникают такие неисправности: термические трещины, кольцевые проточки на поверхности катания колес или повышенный ее износ. Также со временем происходит снижение тормозной эффективности при попадании осадков в зону трения, а также при наличии угольной или торфяной пыли и листьев на поверхности рельсов.
Порядок ремонта тормозного механизма грузового вагона
При КР-2 с вагона снимается тормозное оборудование, все элементы его крепления, а также предохранительные устройства. Все они разбираются и направляются на осмотр, ремонт и эксплуатационные испытания в специальные подразделения. Все сломанные детали тормозной системы заменяются или восстанавливаются. Замене подлежат: воздухораспределители и авторегуляторы. Поступивший в ремонт цилиндр, снаружи тщательно очищается от пыли и загрязнений и осматривается на наличие ржавчины.
Очень важно, чтобы на поверхности корпуса тормозного цилиндра и на его составляющих не было трещин, отколов, изломов, а внутри – коррозии. Однако, если на фланцах корпуса тормозного цилиндра и передней крышке есть не больше двух отколов и при этом отбитая часть захватывает не более 2 соседних отверстий для болтов, то можно приваривать отбитые элементы.
Для разборки, сборки, ремонта, а также эксплуатационных испытаний тормозных цилиндров при КР-2 вагонов применяется специальный стенд. С его помощью очень удобно выполнять разборку и сборку поршневого узла тормозного цилиндра, а также испытывать его на герметичность при рабочем давлении на протяжении трех минут. Благодаря стенду на программном уровне осуществляется:
- контроль параметров проверяемого тормозного цилиндра;
- обмен информацией с базой данных цеховой системы;
- анализ полученных результатов испытаний.
Сетчатые фильтры, которые размещены в передней крышке тормозного цилиндра, надо почистить, помыть, а также продуть с помощью сжатого воздуха. У тех тормозных цилиндров, где нет влагоспускных канавок, сверлится небольшое отверстие.
На герметичность проверяются не только цилиндры, а и рабочие, и запасные резервуары вагонов. В последних режимный валик смазывается. Далее сетки и фильтр промываются, продуваются либо при необходимости заменяются на новые. Вдобавок, проверяется зазор между головкой и опорной плитой. Согласно рекомендациям, он должен быть не больше трех миллиметров. Также проверяется, надежно ли прикреплены основные узлы.
Камера воздухораспределителя проверяется на герметичность с помощью сжатого воздуха под давлением. При этом также проверяются:
- канал тормозного цилиндра с рабочей камерой;
- канал дополнительной разрядки с золотниковой камерой;
- магистральный канал.
Во время деповского ремонта грузовых и пассажирских вагонов составляющие тормозных устройств не снимаются, а восстанавливаются для обеспечения поддержания в работоспособном состоянии всей системы на протяжении межремонтного периода. Таким образом на вагоне ремонтируются:
- тормозные цилиндры,
- коробки зажимов;
- магистральный воздухопровод;
- стоп-краны и др.
Чтобы отремонтировать тормозной цилиндр прямо на вагоне, необходимо снять переднюю крышку вместе с поршнем. В случае, если на штоке поршня отсутствует специальное кольцо для снятия – на него надевается втулка, а в отверстие вставляется валик. Затем уже откручиваются болты. Пружину тормозного цилиндра надо снимать с помощью специального приспособления, обязательно соблюдая все меры безопасности.
Тормозной цилиндр и его элементы очищаются, промываются и протираются, а коррозийный налет удаляется с помощью шлифовальной шкурки. Также необходимо контролировать силовые параметры пружины тормозного цилиндра. Ее заменяют, если она просела более чем на тридцать миллиметров и уже не держит обычную нагрузку.
В процессе сборки рабочую поверхность корпуса тормозного цилиндра надо протереть насухо, а потом смазать тонким слоем с помощью специальной смазки. Также в цилиндре смазывается войлочное кольцо поршня, манжета и сальник. А у рабочих резервуаров смазывается режимный валик.
Рычажную передачу тормозных механизмов грузовых вагонов нужно полностью разобрать, включая съемные элементы стояночного тормоза. Все элементы тормозной рычажной передачи осматриваются на предмет износа, трещин и т. д. и, если нужно, заменяются. Триангели и траверсы испытываются на прочность. После прохождения испытаний на распорке возле струны триангеля ставится специальное клеймо.
Допускается износ рабочих устройств, который составляет не больше пятнадцати процентов от их первоначальной толщины.
При капремонте вагонов таким составляющим тормозной рычажной передачи требуется магнитопорошковый контроль:
- продольных тяг;
- тормозных башмаков;
- поперечных балок и др.
Шарнирные соединения, трущиеся части, а также винты тормозной рычажной передачи смазываются при помощи осевой смазки. Во время сборки на валиках устанавливаются типовые шайбы и шплинты.
Из-за значительной вибрации некоторых узлов рычажной передачи на высокой скорости для уменьшения шумности и увеличения продолжительности срока их службы, предохранительные скобы монтируются на специальных резиновых прокладках. А на длинных тормозных тягах ставятся специальные ограничители вибрации.
Текущий ремонт тормозных механизмов проводятся после отцепки вагона от поезда. При этом тщательно проверяется не только техническое состояние тормозных, но и предохранительных устройств. Износившиеся элементы и узлы заменяются либо ремонтируются.
При ТО тормозных устройств грузовых вагонов, и при их текущем безотцепочном ремонте, все манипуляции проводят в пунктах техобслуживания при подготовке вагонов к рейсу.
Надпись о проведении ремонта тормозных механизмов при деповском и капремонте вагонов не ставится. Периодичность ремонта определяется по надписям, которые были нанесены ранее на кузов, а также на днище котла. Все данные о периодическом ремонте, а также ревизии вагонов заносят в специальную книгу.
При ТО и ремонте тормозного оборудования грузового вагона обязательно нужно соблюдать все необходимые меры для сохранения безопасности. Перед заменой воздухораспределителей, резервуаров, подводящих трубок, вскрытием тормозного цилиндра и регулировкой рычажной передачи нужно обязательно выключить тормоз вагонов, а воздух – выпустить. Менять разъединительные рукава можно, только перекрыв концевые краны смежных вагонов. Запрещено обстукивать рабочую камеру и воздухораспределитель тормозного цилиндра с помощью молотка из металла, а также отвинчивать заглушки резервуаров, которые находятся под давлением.
Тормозное оборудование: периодичность и сроки его ремонта
В основном срок службы грузовых вагонов составляет 20-30 лет. Чтобы обеспечить безопасность движения и выполнить нужный объем перевозок, вагоны нуждаются в контроле исправности в процессе эксплуатации, а также в ремонте. В Российской Федерации и за рубежом сроки ремонта и система техобслуживания вагонов – разные. Это связано с появлением на рынке более надежных и прочных грузовых вагонов. Кроме того, появилось новое современное оборудование, предназначенное для контроля исправности вагонов, а также их тормозных устройств.
Период проведения ревизий, виды техобслуживания, деповского и капитальных ремонтов грузовых и пассажирских вагонов устанавливается ОАО «Российские железные дороги».
Это зависит от пробега вагона или максимально допустимых сроков эксплуатации между проведенными ремонтными работами. К примеру, грузовые вагоны, которые были произведены после 1984 года, проходят капремонт через тринадцать лет после выпуска и через двенадцать лет – после очередного КР. Им требуется деповский ремонт через три года после постройки и спустя два года после ДР и КР или пробега 100 тыс. км. Межремонтные сроки зависят от конструкции грузового вагона, а также от интенсивности его использования.
Учет затрат на ремонт основных средств: проводки
Ремонт основных средств – это процесс, в результате которого происходит восстановление эксплуатационных свойств объектов. Как учитываются затраты на ремонт основных средств в бухгалтерии и какие проводки отражают этот процесс – разберемся в статье.
Объект основного средств может быть восстановлен двумя способами:
- с помощью текущего ремонта;
- с помощью капитального ремонта (реконструкция и модернизация).
Учет затрат в обоих случаях происходит по-разному. Необходимо четко понимать различия в этих процессах, чтобы в будущем не иметь проблем с налоговой инспекцией и не решать споры с проверяющей инстанцией в судебном порядке. Очень важно на начальном этапе определиться, каким образом происходит восстановление объекта.
Если проводится обычный текущий ремонт, то все сопутствующие расходы списываются в затраты организации в текущем налоговом периоде.
Если же проводится реконструкция и модернизация объекта, то все асходы относятся на увеличение стоимости объекта.
Основное отличие ремонта ОС от его реконструкции заключается в том, что в первом случае не происходит изменение технико-экономических показателей объекта. Реконструкция или модернизация — это, в первую очередь, улучшение технических, экономических и производственных показателей объекта.
Ремонт ОС – это устранение неисправностей, повреждений, а также проведение профилактических мероприятий по недопущению преждевременного износа объекта, а также работы, направленные на поддержание рабочего состояния оборудования.
Проведение ремонтных работ, как правило, начинается с формирования смет и плана работы, утвержденного руководителем предприятия.
После ремонта объект принимается к учету на основании акта о приеме-сдаче отремонтированных, реконструированных и модернизированных объектов ОС-3.
Оформление документов ремонта и модернизации
При проведении ремонта основных средств оформляются следующие документы:
- приказ руководителя, который определяет в отношении каких объектов должны быть проведены работы;
- дефектная ведомость, в которой указан характер неисправностей и дефектов, требующих проведения ремонтных работ;
- сметная документация;
- договор подряда в случае, если привлекаются сторонние лица;
- акт о приеме-сдаче отремонтированных основных средств форма ОС-3.
Бухгалтерский учет
Ремонт может быть проведен двумя способами:
- подрядным способом;
-
хозяйственным способом.
В первом случае, ремонтные работы проводится с помощью сторонних подрядных организаций, с которыми заключается договор подряда, после окончания работ подрядчик составляет сметы выполненных работ.
Во втором случае, ремонтные работы выполняется собственными силами.
Затраты на ремонт объектов основных средств относятся на счета учета производственных издержек, то есть включаются в себестоимость продукции с помощью проводок: Д20 (23, 25, 26, 44) К10 (60, 70, 69).
Если же расходы составляют значительную сумму, то организация может осуществлять ремонтные работы за счет заранее сформированного резерва. Этот резерв образуется путем постепенного включения определенных сумм в состав себестоимости продукции в течении длительного времени, при этом выполняются проводки Д 20 (23, 25, 26) К96, где счет 96 именуется «Резерв предстоящих расходов», на котором по кредиту и формируется резерв. Сумма ежемесячных отчислений на формирование резерва определяется, как 1/12 от годовой стоимости ремонта по смете.
Если в конце года по кредиту счета 96 остались средства (то есть сумма, необходимая для ремонта оказалась меньше сформированного резерва), то оставшиеся средства списываются на 91 счет проводкой Д96 К91/1, таким образом счет 96 закрывается.
Если суммы резерва не достаточно для проведения ремонтных работ, то недостающие средства либо получают с помощью дополнительной проводки по увеличению резервного фонда Д20 К96, либо списывают эту сумму на издержки проводкой Д20 К10, 60, 70.
Проводки по учету расходов на ремонт основных средств:
Источник: Простая бухгалтерия
шагов для разборки и повторной сборки запчастей с легкостью
BY: Deanna Sclar и
Обновлены: 05-25-2021
Из книги: Auto Report for Dummies, 2-е издание
Auto Repair For Dummies для Dummies для Dummies для Dummies для Dummies для Dummies для Dummies.
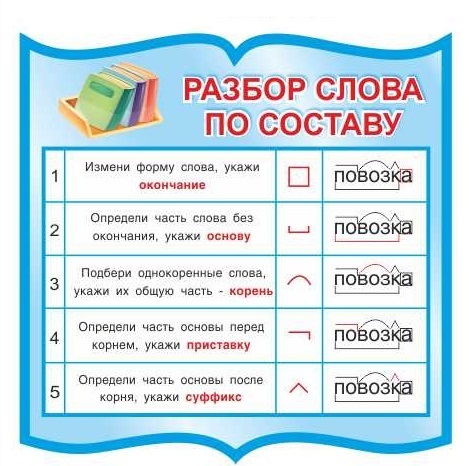
Исследовать книгу Купить на Amazon
При выполнении ремонта вам нужна процедура, которая поможет вам разобрать и собрать все обратно. Процедура здесь подходит для ремонта, который требует, чтобы вы что-то разобрали и снова собрали — спущенные шины, тостеры, велосипеды, что угодно.
Выделите себе достаточно времени. Если дела идут плохо, выпейте немного воды или чашку кофе. Вы можете получить совершенно новую перспективу, когда вернетесь к работе. Ограничьте отвлекающие факторы: включите автоответчик или снимите трубку телефона, держите подальше детей и собаку и расслабьтесь. Если вы попали в затруднительное положение, сядьте тихо и подумайте об этом — не паникуйте. Если детали подходили друг к другу раньше, они будут соответствовать друг другу снова.
Выложи чистой, безворсовой тряпкой на плоской поверхности, достаточно близко, чтобы до нее можно было дотянуться без необходимости вставать или идти к ней.
Вы будете класть каждую часть на эту тряпку, когда будете ее снимать. Следовательно, тряпка не должна находиться в месте, где на нее может попасть масло, пыль или что-то еще и запачкать детали. Если вы планируете использовать что-то, что выдувает воздух для очистки, оставьте достаточное количество тряпки, чтобы сложить ее поверх лежащих на ней частей.
При снятии каждой детали отмечайте (на бумаге, чтобы не забыть), откуда взялась эта деталь, как она была прикреплена и насколько крепко она была закреплена или привинчена.
Большинство любителей кладут вещи обратно очень плотно, в надежде, что деталь не слетит. Но некоторые вещи, такие как болты, которые удерживают прокладки на месте, не следует затягивать слишком сильно, потому что, например, резьба болтов может быть сорвана или прокладка может деформироваться, что позволит выйти наружу тому, что она держит. Полезно делать заметки о том, насколько сложно было удалить каждую вещь. «Не затягивайте слишком сильно» или «Убедитесь, что это надежно».
Когда вы снимаете каждую часть, кладите ее на тряпку по часовой стрелке, чтобы каждая часть указывала в том направлении, в котором она была до того, как вы ее сняли.
Это ключ ко всей системе. Когда вы будете готовы собрать вещи, расположение и направление каждой детали подскажет вам, когда ее нужно положить обратно и как она была ориентирована.
Если вы делаете заметки, присвойте каждой части номер, указывающий порядок, в котором вы ее удаляли — Часть № 1, Часть № 2 и т. д.
Можно даже малярным скотчем пронумеровать детали, если боитесь, что тряпку можно случайно сдвинуть. Также обратите внимание, к чему была прикреплена каждая часть; например, «Часть № 6: зацепите конец руки за левый хук за ручку справа от Части № 7». Добавьте эскиз, если это поможет.
Если вы работаете систематически и понимаете функцию каждой детали, у вас не останется лишних гаек и болтов в конце работы.
Когда вы будете готовы собрать все обратно, начните с последней снятой детали и двигайтесь против часовой стрелки по частям на тряпке.
Если вы пронумеровали части, они должны идти в обратном порядке.
Эта статья из книги:
- Ремонт автомобилей для чайников, 2-е издание,
Об авторе книги:
Дина Склар — известный специалист по ремонту автомобилей. Она появлялась в сотнях радио- и телешоу, включая шоу NBC Today и NBC Nightly News . Склар читает лекции на международном уровне об экологическом воздействии транспортных средств и активно продвигает программы солнечной энергии в жилых домах. Склар также является автором книги «Покупка автомобиля для чайников».
Этот артикул находится в категории:
- Общий ремонт и техническое обслуживание автомобилей,
КАК РАЗБОРАТЬ И РЕМОНТИРОВАТЬ ДВИГАТЕЛЬ PERKINS, ШАГ ЗА ШАГОМ (ЧАСТЬ 1)
286 / 07.
Двигатели Perkins являются одними из наиболее часто используемых в промышленности сельскохозяйственных и строительных машин. Они известны своей надежностью, долговечностью и достаточной мощностью для выполнения любой работы.
После многих лет использования любой двигатель может начать проявлять механические неисправности, связанные с износом некоторых его частей, хотя каждая часть двигателя Perkins может быть заменена, для выполнения этих процедур требуются базовые знания в области автомобильной механики.
В Maq Parts имеется широкий ассортимент всех запасных частей и запасных частей, которые могут понадобиться вашему двигателю Perkins. В этом посте мы шаг за шагом объясним, как его разобрать и как проверить каждую из частей двигателя Perkins.
ПРИМЕЧАНИЕ:
Мы настоятельно рекомендуем производить разборку и ремонт двигателя Perkins только при наличии необходимых инструментов и опыта. Помните, что двигатель — это очень сложная машина, каждую деталь нужно аккуратно снимать и устанавливать обратно в том же порядке, в каком она была снята.
Если во время разборки двигателя Perkins у вас нет необходимых для этого инструментов или вы не считаете, что обладаете базовыми знаниями в области автомобильной механики для выполнения процедур, мы настоятельно рекомендуем вам обратиться к доверенному механик, чтобы не ошибиться. ошибка, которая может сломать любую из частей или повредить работу вашего двигателя.
ИНСТРУМЕНТЫ
Для беспроблемного выполнения всех процедур вам потребуются следующие инструменты:
- Набор отверток
- Набор ключей с трещоткой
- Кабель для тяжелых условий эксплуатации или С-образные зажимы
- Резиновый молоток или средний молоток
- Клещи для замков
- Клещи
- Сферический алексометр
- 5 Тонкий штифт
- Кусачки
- Вольтметр или мультиметр
- Шаровой молоток
- Рычаг
- Щуп
- Съемник клапана
- Микрометр
- Автомобильные пандусы
- Гидравлический домкрат
ПРОЦЕДУРА РАЗБОРКИ ДВИГАТЕЛЯ PERKINS
Если у вас уже есть все инструменты, упомянутые в предыдущем разделе, теперь мы можем начать: его, переверните его так, чтобы его положение было инвертировано.
Шаг 2 : Затем с помощью отверток необходимо открутить все винты, удерживающие крышку двигателя, а затем снять ее.
Шаг 3 : После снятия крышки картера первое, что вы видите, это масляный насос двигателя с выступающим масляным фильтром, он отличается формой металлической сетки, которая отвечает за предотвращение попадания загрязнений, которые могут повредить двигатель. насос.
Шаг 4 : Первая часть, которую мы можем извлечь, это масляный насос, для этого мы должны ослабить «болты» или болты, которые его держат, с помощью набора кубиков.
Шаг 5 : Как только мы вытащим масляный насос, мы увидим крышки шатунов, в зависимости от положения двигателя вы заметите, что они расположены парами, в случае 4-цилиндровых двигателей шатун 1 будет находиться в том же положении, что и 4, а 2 — в том же положении, что и 3. Для 6-цилиндровых двигателей шатун 1 будет в том же положении, что и 6, 2 — в том же положении, что и 5, а 3 — в том же положении, что и 4.
Помните, что каждый шатун должен быть размещен точно в одном и том же положении, если они не имеют заводских номеров, пометьте их для идентификации.
Этап 6 : Далее с погремушками ослабьте крышки шатунов. Как только шатуны ослабнут, осторожно ударьте по ним резиновым молотком, чтобы освободить их и снять.
Шаг 7 : Как мы упоминали в шаге 5, шатуны парные, когда вы закончите извлекать первые 2, вам нужно будет немного повернуть коленчатый вал, чтобы два других, которые были скрыты, были выше, и вы повторите шаг 6 со следующими двумя шатунами.
Шаг 8 : После того, как мы сняли все крышки, ударьте резиновым молотком по шатунам сзади, медленно проталкивая поршень внутрь цилиндра, пока кольцо, поршень и шатун не выйдут полностью.
Шаг 9 : После того, как мы сняли все шатуны с двигателя, приступаем к генеральной очистке блока цилиндров, для этого вам понадобятся специальные чистящие средства для двигателей и, таким образом, вы сможете удалить масло, нагар , среди прочих.
Шаг 10 : Когда шатуны двигателя сняты, мы можем приступить к снятию поршней один за другим, постарайтесь снять их с той же стороны, с которой были сняты шатуны.
ЭТАП 11, ИСПОЛЬЗОВАНИЕ АЛЕКСОМЕТРА : После того, как каждый из поршней был снят, рекомендуется выполнить измерение внутреннего диаметра цилиндров с помощью алексометра.
Целью данного шага является измерение износа в цилиндрах двигателя, учитывая, что стук, возникающий при сгорании, постепенно изнашивает цилиндры, за счет этого между верхней частью цилиндров создается небольшая ступенька.
Эта процедура состоит из измерения шага, чтобы узнать износ двигателя, чем глубже или выраженнее шаг, тем больше будет износ двигателя.
1 . Подбираем удлинитель под диаметр цилиндра нашего двигателя. Этот диаметр можно найти на листе производителя. Вы должны учитывать, что диаметр выбранной вами детали должен иметь общую длину головки (включая максимальный допуск) немного больше, чем номинальный диаметр, указанный в листе производителя двигателя, это гарантирует, что трассеры находятся в постоянном контакте с стенки цилиндра.
2 . Поместите алесометр перпендикулярно цилиндру и отрегулируйте зажим или фиксирующую гайку по стенкам цилиндра.
3 . Измерьте микрометром нормальный диаметр цилиндра.
4 . Вставьте головку алесометра в цилиндр и откалибруйте циферблатный индикатор до нуля, осторожно перемещая алесометр колебательными движениями, пока не получите минимальное измерение, которое мы возьмем в качестве эталона. В этом минимальном измерении мы будем калибровать ноль.
5 . Снимите алесометр с микрометра и вставьте его в первый измеряемый цилиндр. Убедитесь, что нутромер входит в цилиндр в наклонном положении, так как это не повредит щупы.
6 . Оказавшись внутри цилиндра, мы совмещаем ручку алесометра с осью цилиндра и снимаем показания стрелочного индикатора.
7 . Снова продолжаем колебательно двигать алесометр до тех пор, пока не найдем точку перегиба, являющуюся точной точкой измерения. Если эта точка совпадает с предшествующим нулем на шкале, сравниваемая мера будет точно совпадать. Если бы, с другой стороны, точка перегиба совпадала, например, с 5 на шкале, сравниваемое измерение было бы на 0,05 мм больше заданного измерения.
8 . Чтобы извлечь флексометр из цилиндра, мы должны снова сделать это с наклоном корпуса, чтобы не повредить стрелочный индикатор.
Шаг 12 : Получив диаметр каждого из цилиндров вашего двигателя, его необходимо сравнить с исходным диаметром, это можно найти в данных производителя вашего двигателя Perkins.
Считает, что для получения достоверных результатов необходимо произвести достаточное количество измерений. Рекомендуется провести как минимум три измерения на трех разных высотах (всего девять для каждого цилиндра), это даст превосходную оценку степени износа измеряемого цилиндра.
ИСПРАВЛЕНИЕ ИЛИ ЗАМЕНА ДЕТАЛЕЙ
В зависимости от полученных результатов по сравнению с данными производителя можно будет определить, можно ли решить проблему износа двигателя с помощью исправления или необходимо заменить кольца.